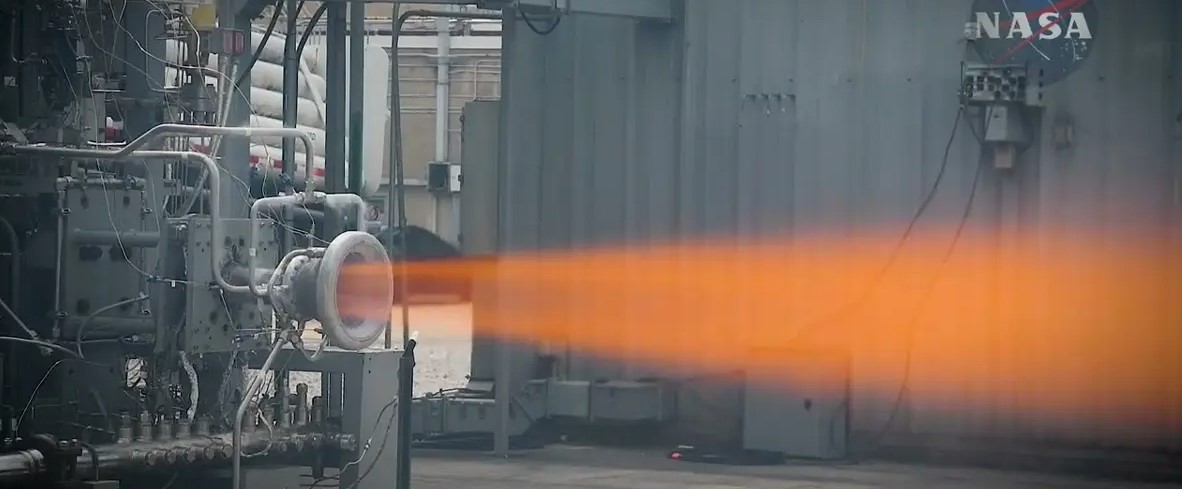
One of the key trends in the space industry is to reduce the cost of sending crews and payloads into space by using new technologies and processes. Space agencies are striving to find new ways to make missions more cost-effective. NASA has successfully tested an aluminum rocket engine nozzle made using the 3D printing process. The technology makes it possible to produce aluminum components as a single unit, which makes the material more practical and reliable, and reduces production time.
Additive manufacturing (3D printing) has made a real revolution. Unlike traditional methods, where a significant portion of raw materials goes to unavoidable waste during production, 3D printing creates components to order, layer by layer. This process produces virtually no waste and is fast, economical and efficient. Previously, 3D printing was mainly used for modeling and prototyping, but now the scope of application includes the aerospace industry.
NASA has developed the aluminum nozzle in collaboration with Elementum 3D, one of the leading 3D printing companies. Compared to other metals, aluminum has a lower density and makes it possible to create high-strength and lightweight components. However, in traditional production, a rocket nozzle can require thousands of individually connected parts. This makes aluminum impractical, as it has low resistance to extreme temperatures and a tendency to crack during welding. The RAMFIRE (Reactive Additive Manufacturing for the Fourth Industrial Revolution) process eliminates this problem by producing aluminum components as a single unit, which significantly reduces production time.
The nozzles have small internal channels that help to cool them, preventing them from melting. The RAMFIRE 3D printer and the process of forming parts were developed by another NASA commercial partner, RPM Innovations. This company specializes in the Directed Energy Deposition (DED) method, in which layers of powdered alloy are deposited and fused using lasers.
Two RAMFIRE nozzles based on this technology have been successfully tested at the Marshall Space Flight Center’s Huntsville test site. The nozzles have been tested using liquid oxygen (LOX) and liquid hydrogen (LH2), as well as combinations of LOX with liquid methane at pressures exceeding 5690 kilopascals. This is higher than expected during a rocket launch. In total, the nozzles underwent 22 launch tests and operated for more than 10 minutes, demonstrating their ability to withstand the harsh conditions during rocket launch and in outer space.
NASA first demonstrated the effectiveness of 3D-printed components in March 2023, when Relativity Space conducted a test launch of its Terran 1 rocket from the Cape Canaveral Space Force Station in Florida. This test rocket was the first to be made entirely of 3D-printed parts. The motors were made of an innovative Glenn Research Copper alloy and could withstand temperatures approaching 3315 °C, which is 40% higher than traditional copper alloys.
In addition to rocket nozzles and engines, RAMFIRE also manufactured a 91 cm diameter aerodynamic nozzle that includes components for use with cryogenic propellants. These innovations are important for NASA’s Moon-Mars program, which includes the Artemis mission and the return of astronauts to the Moon, as well as the creation of lunar infrastructure necessary for organizing manned missions to Mars. An integral part of this program is sending larger cargoes to the Moon, Mars and other places in deep space, as well as the possible creation of rocket parts outside the Earth.