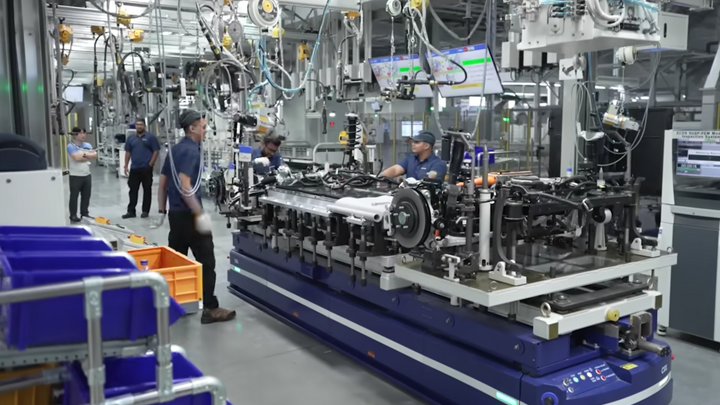
For now, it is an experimental plant, and in addition to humans and robots, there are also robopets working here.
Inside, Hyundai’s Singapore electric car plant resembles scenes from some distant utopian future. Spot, a Boston Dynamics robot dog, walks around conducting quality checks, autonomous robotic arms carefully tighten bolts and install windshield wipers, and self-driving ground vehicles move components and electric vehicles to different areas of the plant.
With so much autonomous equipment, human presence is almost unnecessary. Sixty percent of the tasks are done by robots, said one of our members who visited the plant in Singapore last month. And only 100 employees are needed to produce 30,000 cars a year.
This is not a typical car plant. This is a “microfactory” aimed at rethinking production by creating cars in a “cell” rather than on a traditional production line. Interestingly, Hyundai’s microfactory, as the name suggests, is much smaller than traditional car plants.
For example, Tesla’s gigafactory in Texas has an area of more than 930,000 square meters, which is roughly equal to 100 football fields, and has the capacity to produce more than 250,000 electric vehicles per year.
Hyundai’s plant in Singapore, one of three production bases for the Ioniq 5 besides South Korea and Indonesia, covers only 86,000 square meters with an annual production capacity of 30,000 vehicles.
Generally, an assembly line is where a vehicle is assembled step by step as it moves along a conveyor belt. Humans and robots work in tandem to accomplish these tasks. The Hyundai model based on cells is not fundamentally different, but provides more flexibility.
In the chambers, robots install car components before moving on to the next zone. The key difference is that the cells can be programmed with specific instructions, ranging from installing components for different variants of the same car or working on a completely different model. Traditional assembly lines will require significant re-equipment to be able to be adaptive.
However, the plant in Singapore is more of a technological showcase, designed for urban areas where space is at a premium;. It is unlikely that this revolutionary production will be implemented worldwide in the near future, especially in the United States after the trade union strikes.
However, such a plant is worrisome, and it is especially disappointing to know that only 100 people work at a plant that can produce 30,000 electric cars a year. Is Hyundai going to build more such facilities? Will others copy Hyundai? We don’t know yet. And we hope not. But with the industry increasingly moving towards artificial intelligence and automation globally to improve efficiency and reduce costs, this plant is definitely worth a look.